
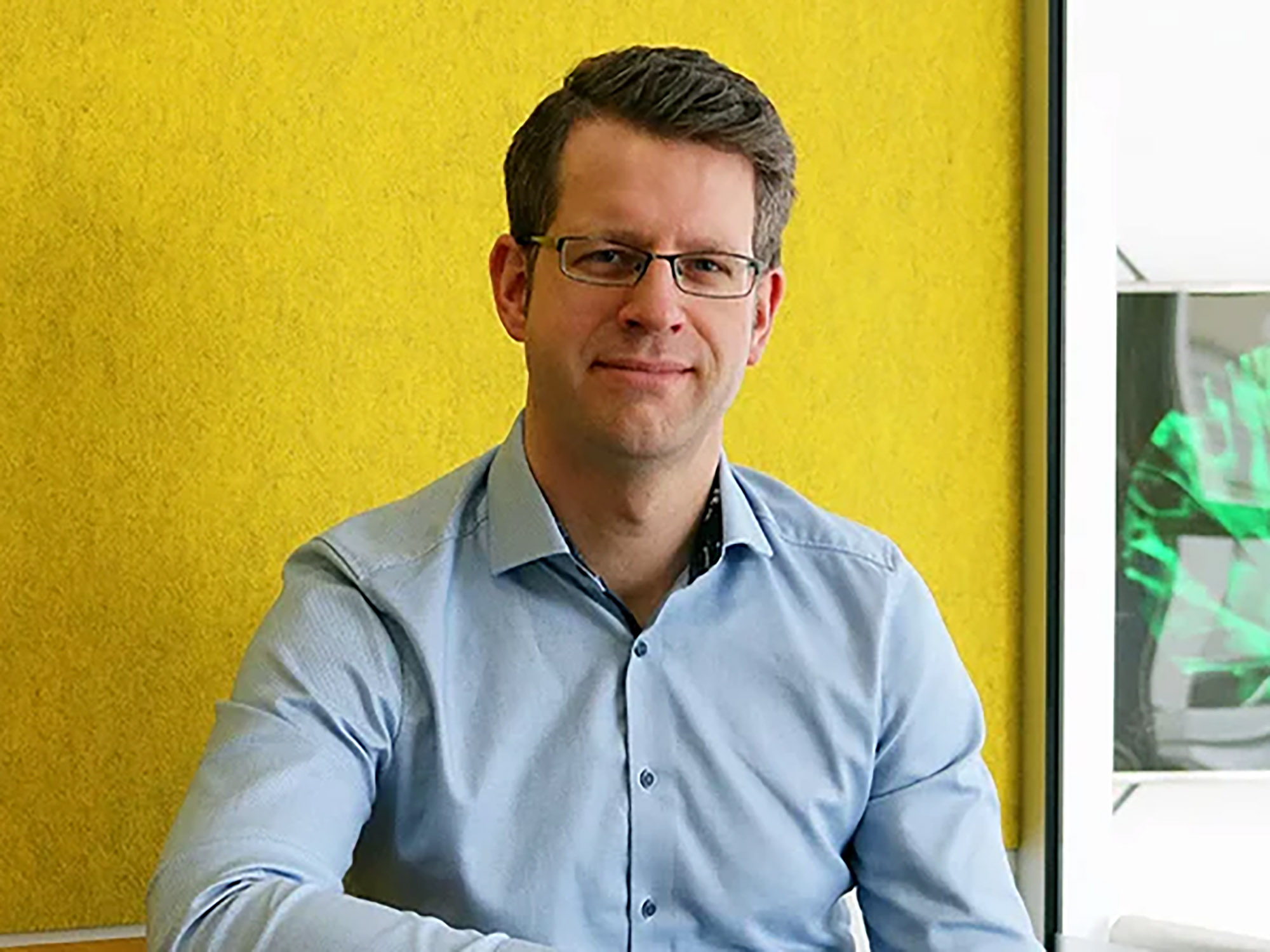
Flottweg’s Dr Mathias Aschenbrenner: Unlocking value in plant protein side streams
As global demand for plant-based protein continues to rise, producers face mounting pressure to maximize efficiency, minimize waste, and ensure every part of the raw material is used productively. According to Dr Mathias Aschenbrenner, Sales Engineer at Flottweg, creating a viable business case for customers increasingly depends on how effectively companies manage side streams in plant protein production.
“The most important criterion for success is creating a good business case for the customer,” said Dr Aschenbrenner. “That’s why it is becoming increasingly important to utilize byproducts and to find new, alternative sources of raw materials.”
He noted that while extracting protein remains the priority for many producers, the other components of crops such as peas – namely starch and fiber – also offer commercial value if handled appropriately. For example, the dry matter of a pea typically contains around 25% protein, 50% starch, and 20% fiber. Ignoring the latter two not only wastes resources but also weakens the financial model.
“To establish a good business case, we need to take a holistic approach to our raw materials,” said Dr Aschenbrenner. “It would be an absolute waste of raw materials and make poor business sense to not use the other 75%.”
To achieve this, Flottweg applies mechanical separation techniques to recover valuable starch and fiber from the production process. A centrifugal mesh is used to separate starch from fiber, and a belt press then dewaters the fiber, preparing it for processes such as drying. Meanwhile, the starch can either be dewatered immediately using a decanter or further refined via hydrocyclones. The refining process involves washing the starch in multiple stages to achieve the desired level of purity, which varies depending on its intended application – whether in fermentation, food, or industrial sectors.
“Starch is a very versatile product,” he explained. “The required degree of purity depends on the application.”
Dr Aschenbrenner also highlighted the growing importance of alternative raw materials – those not produced specifically for protein extraction, but that are generated as waste or side products in other processes. Two key examples are press cakes from oil production and brewer’s grains from the brewing industry. Although rich in protein, these byproducts are mostly used as animal feed due to limited processing alternatives.
“Since these raw materials are already available in large quantities, it can be very lucrative to extract this protein to generate additional value,” he said.
Flottweg’s approach to value chain optimization begins early. The company collaborates closely with customers during the pre-engineering phase to develop tailored solutions based on the specific priorities of each project. This phase includes detailed concepts such as layout planning and mass balancing, helping customers gain a full understanding of the process and its outcomes before implementation.
“In the production of plant protein, our customers’ priorities vary greatly from case to case,” said Dr Aschenbrenner. “That’s why we develop custom-made solutions with our customers right from the start.”
Flottweg’s centrifuges, including its proprietary Sedicanter, play a central role in ensuring consistent and efficient processing – even when the composition or volume of byproduct streams fluctuates. According to Dr Aschenbrenner, the flexibility of the company’s separation technologies enables stable operations across a range of conditions.
“Particularly with byproduct streams, it is common to have fluctuations in composition and quantity,” he said. “Our smart separation solutions adapt to these conditions and ensure stable processes even under adverse conditions.”
With decades of experience in separation technology, Flottweg supports both modular equipment and turnkey systems for plant protein production. Its decanter centrifuges are used across nearly every stage of the protein extraction process, ensuring that not only proteins but all potential value streams are captured.
“With the help of the Flottweg system solutions, maximum yields of top-quality vegetable protein can be extracted efficiently and without wasting resources,” Dr. Aschenbrenner said. “We offer our customers everything from a single source – from the initial idea, to execution of the project, all the way to after-sales service.”
If you have any questions or would like to get in touch with us, please email info@futureofproteinproduction.com