
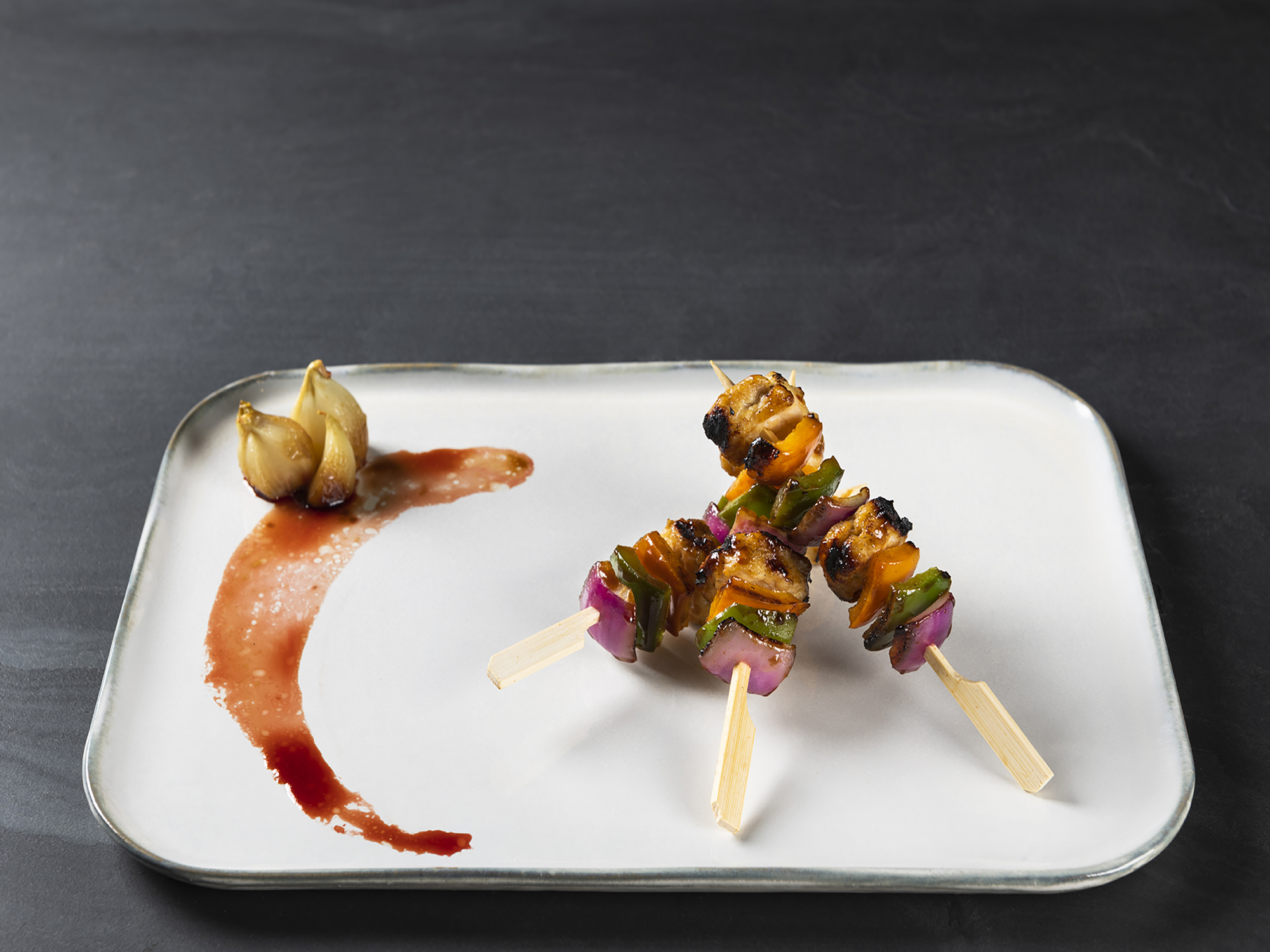
SuperMeat's forward-facing LCA highlights 50% decrease in carbon footprint of chicken, the most efficient animal protein
SuperMeat, a food-tech company dedicated to supplying the world with high-quality cultivated meat, has shared industry-first, forward-looking projections for cultivated chicken based on its landmark continuous production process, outperforming the ambitious benchmarks set for conventional chicken at the start of the next decade.
The Life-Cycle Analysis (LCA) was conducted by CE Delft, an independent sustainability research and consultancy firm, to evaluate the anticipated environmental impact of a large-scale production of SuperMeat’s cultivated chicken, offering a glimpse into the future of sustainable meat production.
The assessment provides a detailed comparative analysis between SuperMeat’s 100% cultivated chicken and the most sustainably produced traditional chicken aspired for the outset of the 2030s.
SuperMeat’s cultivated chicken is projected to achieve a carbon footprint approximately 50% lower than the ambitious benchmarks set for conventional chicken production, when integrating renewable energy sources and sustainable production practices in both conventional and cultivated production methods. Even under the reliance on standard grid electricity, a 27% reduction in the carbon footprint of SuperMeat's chicken is achieved, in comparison to the ambitious conventional chicken benchmark.
This analysis not only showcases the advantages of cultivated meat compared to conventional methods, but shows, for the first time, that cultivated meat could drastically improve the most carbon-efficient form of animal protein available today – chicken – in carbon efficiency and across numerous other measures.
Among the findings, in terms of reduced environmental impact, SuperMeat’s cultivated chicken marks a significant 47% reduction in carbon footprint, a 64% decrease in fine particulate matter formation, an 85% lessening in terrestrial acidification, and a 90% cutback in land use compared to traditional chicken farming.
Meanwhile, in terms of enhanced feed-to-meat efficiency, SuperMeat's chicken product exhibits a lower Feed Conversion Ratio (FCR) than conventional meats, demonstrating superior efficiency in transforming feed into meat. Specifically, SuperMeat's FCR is estimated at around 1 vs. 2.8 for chicken, almost three times more efficient.
SuperMeat’s continuous production process will be instrumental in achieving the expected sustainability outcomes for its cultivated chicken. The foundation of this analysis is based on practices currently in place at SuperMeat's pilot plant, underscoring the current effectiveness and feasibility of this approach. The continuous production process allows for significantly higher yields – up to nine times greater than a fed-batch process based on SuperMeat’s data – and is more energy-efficient than fed-batch processes. Moreover, the adoption of high cell densities and the use of spent media in SuperMeat’s process contribute to a favorable feed-to-kilogram conversion rate. These breakthroughs in cellular agriculture are expected to enable SuperMeat to set these sustainability standards when producing at a commercial scale.
"Efficiency in meat production is no longer a goal; it's a necessity,” commented SuperMeat’s CEO Ido Savir. “Our pilot plant is the proving ground for SuperMeat's vision of efficiency and sustainability. Through continuous production, we've showcased the potential to dramatically increase yields while reducing our environmental footprint, a testament to our dedication to advancing meat production."
SuperMeat remains dedicated to pioneering advancements in sustainable meat production, and will use this LCA as a strategic guide for planning its large-scale production facilities, with a focus on incorporating renewable energy, establishing a sustainable supply chain and enhancing production processes.
If you have any questions or would like to get in touch with us, please email info@futureofproteinproduction.com