
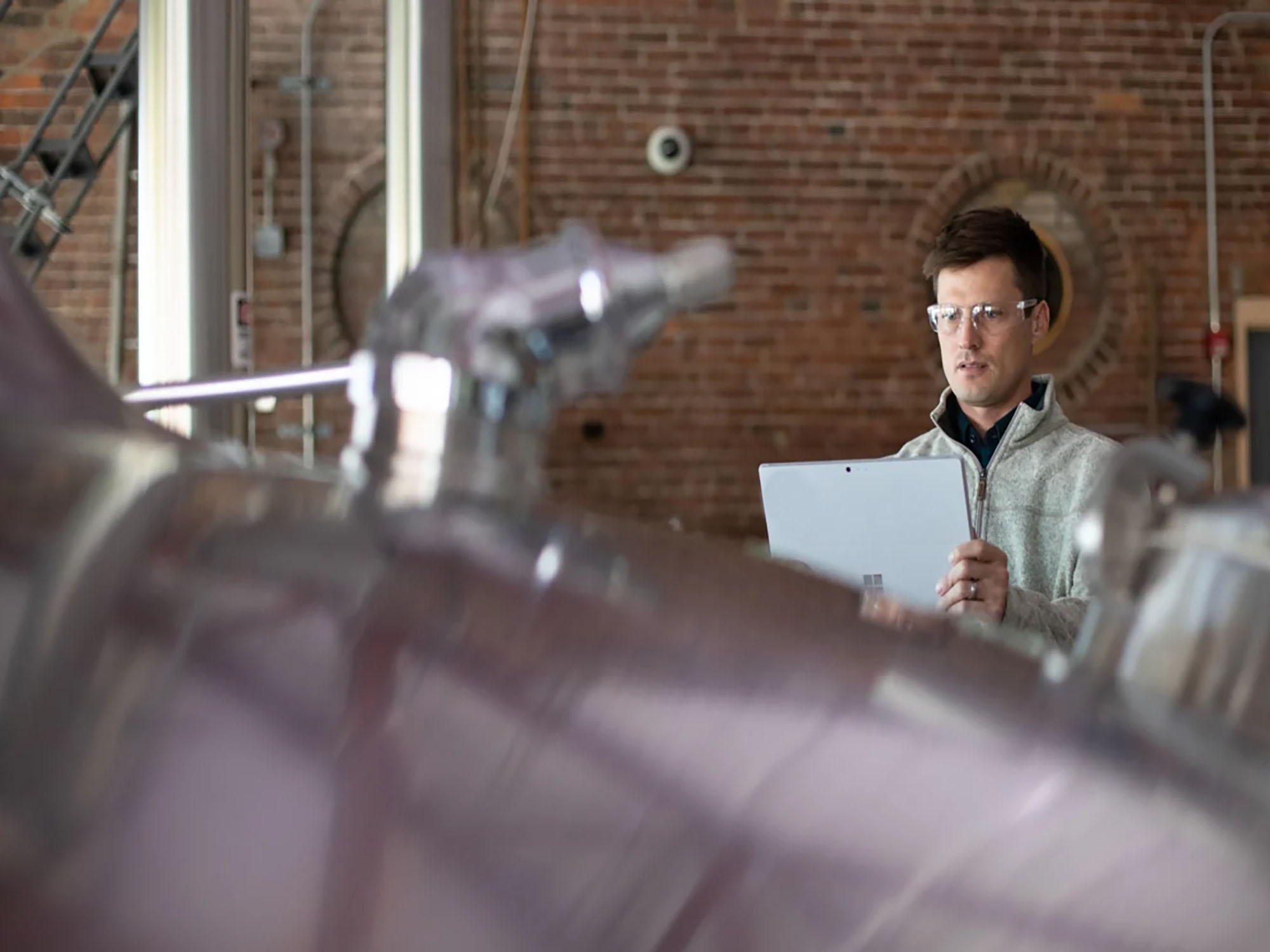
Rockwell helps alternative protein manufacturers meet global demands
Rockwell Automation, in collaboration with its Gold System Integrator Partner E Tech, is helping alternative protein manufacturers scale operations efficiently to meet growing global demand. By integrating advanced automation technology, Rockwell is enabling producers to transition from small-scale testing to commercial production while maintaining quality, sustainability, and cost efficiency.
With the global population expected to surpass 10 billion people, sustainable food production has become a priority. Alternative proteins—whether derived from plants, cultivated cells, or fermentation—offer a promising solution. However, scaling these technologies to mass production remains a major challenge.
A key hurdle for alternative protein facilities is transforming a laboratory-proven concept into large-scale manufacturing. Rockwell Automation is supporting FDA-approved alternative protein production sites, ensuring that these novel food solutions match the taste and affordability of conventional products while minimizing environmental impact.
One essential factor in achieving scale is data-driven process optimization. Early adoption of data collection, recording, and analysis technology enables better product testing and predictive modeling. Rockwell’s automation solutions streamline this transition, allowing manufacturers to make informed decisions based on digital inputs rather than manual trial-and-error testing.
Rockwell’s PlantPAx Distributed Control System (DCS) provides a fully scalable, plant-wide solution tailored to the unique needs of alternative protein manufacturers. Unlike traditional control systems, PlantPAx integrates seamlessly with existing plant infrastructure, offering advanced process optimization, real-time data visualization, and predictive analytics. This system ensures consistent product quality while improving energy efficiency and resource management, which are critical factors for sustainable protein production.
The FactoryTalk Batch software enhances Rockwell’s automation framework by enabling flexible, recipe-driven batch processing. This advanced batch management system provides manufacturers with the ability to optimize ingredient mixing, fermentation cycles, and processing times, ensuring precise control over production variables. FactoryTalk Batch also supports electronic batch recording, reducing compliance risks and ensuring traceability, which is essential for regulatory adherence in food production.
By integrating PlantPAx DCS and FactoryTalk Batch, alternative protein producers can transition from manual testing to fully automated operations, significantly reducing trial-and-error costs. These technologies enable seamless scaling from pilot to full-scale production with predictive analytics and automated adjustments. Optimized resource utilization minimizes waste and improves ingredient efficiency. Enhanced quality control through real-time monitoring and automated compliance tracking ensures consistent product performance. Reduced production costs maximize throughput and minimize downtime, creating an efficient and scalable production environment.
If you have any questions or would like to get in touch with us, please email info@futureofproteinproduction.com