
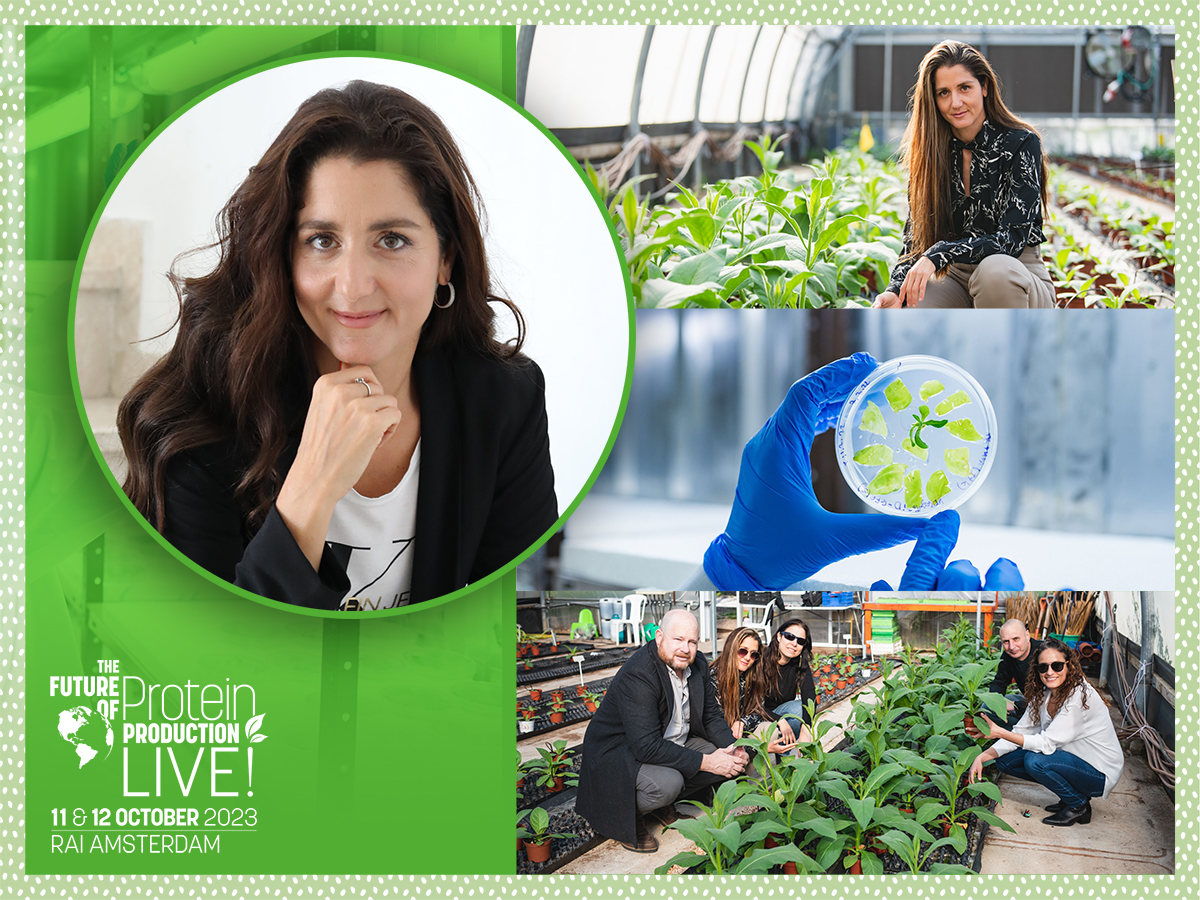
Could plant molecular farming be a fundamental building block for a commercially viable cultivated meat industry?
In getting to know all +65 speakers taking part in The Future of Protein Production LIVE!, we are exposing the future trends and solutions that will propel alternative proteins into the mainstream. Here we speak with BioBetter’s Dr Dana Yarden
Dr Dana Yarden is the Co-founder of BioBetter, the Kiryat Shmona, Israel-based company that has developed a protein manufacturing platform to address the fast-growing demand for growth factors in the cell ag industry, specifically for use in cultivated meat.
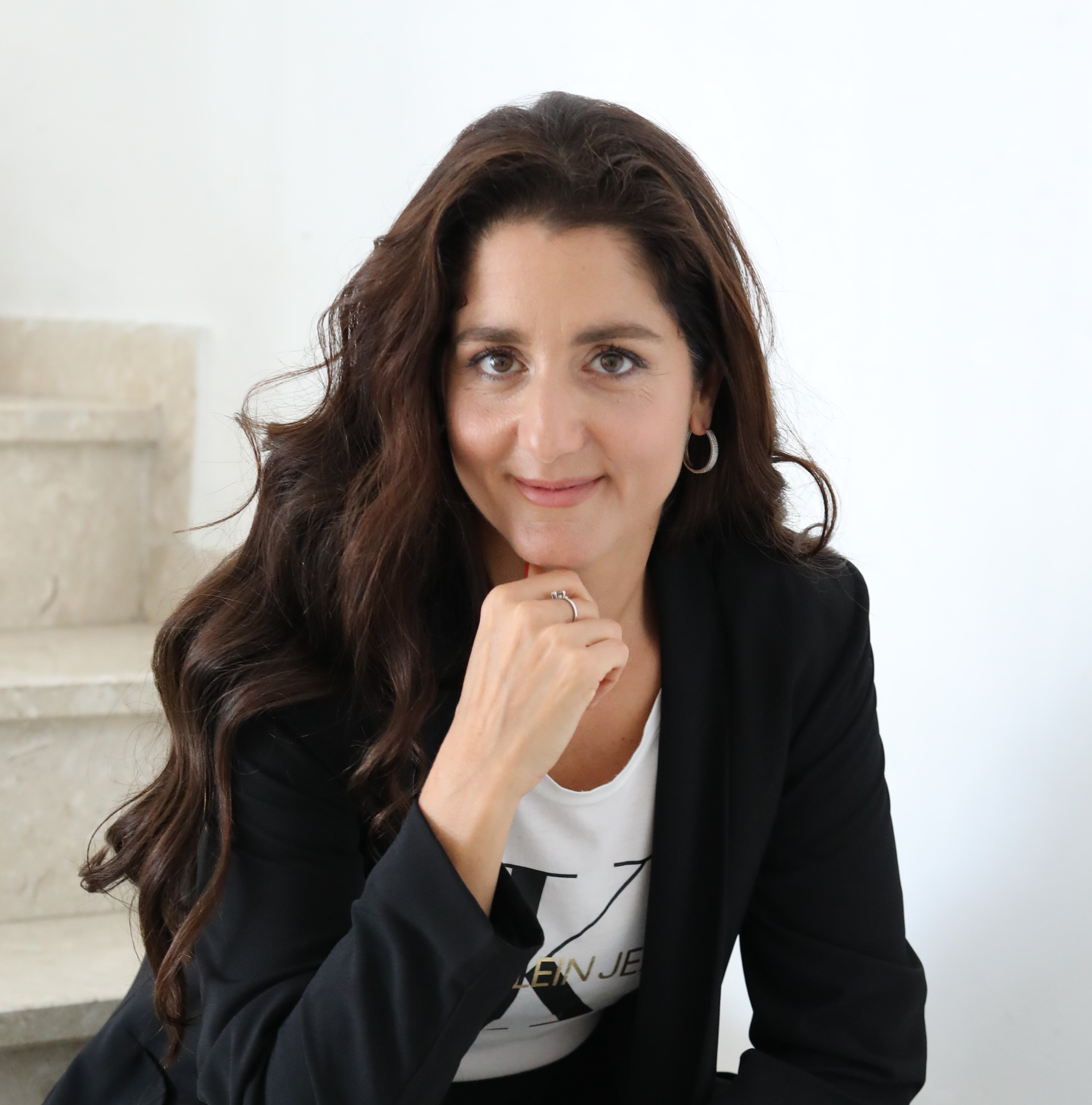
Appearing at The Future of Protein Production LIVE! on 11/12 October, Yarden is one of +65 expert speakers who will be showcasing real-world solutions to the myriad challenges involved in taking alternative protein-derived foods from pilot to plate. In the field of cultivated meat – widely touted to be the ultimate sustainable and ethical alternative to conventional meat – the high cost and low availability of growth factors remains one of the most significant challenges.
Currently available technologies cannot produce growth factors in sufficient volumes and at costs low enough to support commodity production. Indeed, according to some estimates, the cost of cell-culture media made up anything between 55-95% of the marginal cost of manufacturing cultivated meat, with 99% of that cost attributed to growth factors alone. “They are expensive and rely on animal-derived products, which until now has hindered the scalability and affordability of cultivated meat,” Yarden feels. To overcome this, though, researchers are exploring alternatives, such as plant-based or microbial sources, as well as the development of animal-free media.
BioBetter’s fascinating innovation unplugs the bottleneck by using plants as bioreactors. “Our flexible, novel molecular farming production platform using tobacco plants as bioreactors enables the production of growth factors in unlimited capacity, and at ultra-low COGS [Cost of Goods Sold] of around US$1/g,” Yarden explains.
These are impressive claims, especially given a 2021 GFI report that revealed a ideal scenario would be a target of around US$4/g. So, how has BioBetter managed to steal a march?
The idea was first conceived in 2012, leveraging the IP and know-how of Professor Oded Shoseyov from the Hebrew University of Jerusalem. The company itself was founded in 2015 by Professor Shoseyov, Avi Tzur, and Yarden. By 2017, BioBetter was fully operational under the leadership of CEO, Dr Amit Yaari, with a focus on biosimilars for the pharmaceutical market.
“However, during the Covid-19 pandemic, it became challenging to secure funding,” recalls Yarden. Around about that time, though, she and her colleagues were approached by a company in the cultivated meat sector, which wanted to utilize BioBetter’s platform to produce growth factors essential to cultivated meat.
We understood that producing a food product would be easier from a regulatory standpoint and technologically a bit more straightforward. Additionally, without clinical trials, the road to market would be much shorter
“Intrigued by the concept, we pivoted the entire company and raised funds for a proof of concept to produce insulin, transferrin, and FGF2 in tobacco plants,” she reveals. “We understood that producing a food product would be easier from a regulatory standpoint and technologically a bit more straightforward. Additionally, without clinical trials, the road to market would be much shorter. So, in 2021, we successfully achieved this proof of concept and began building our network and position within the food-tech community in 2022.”
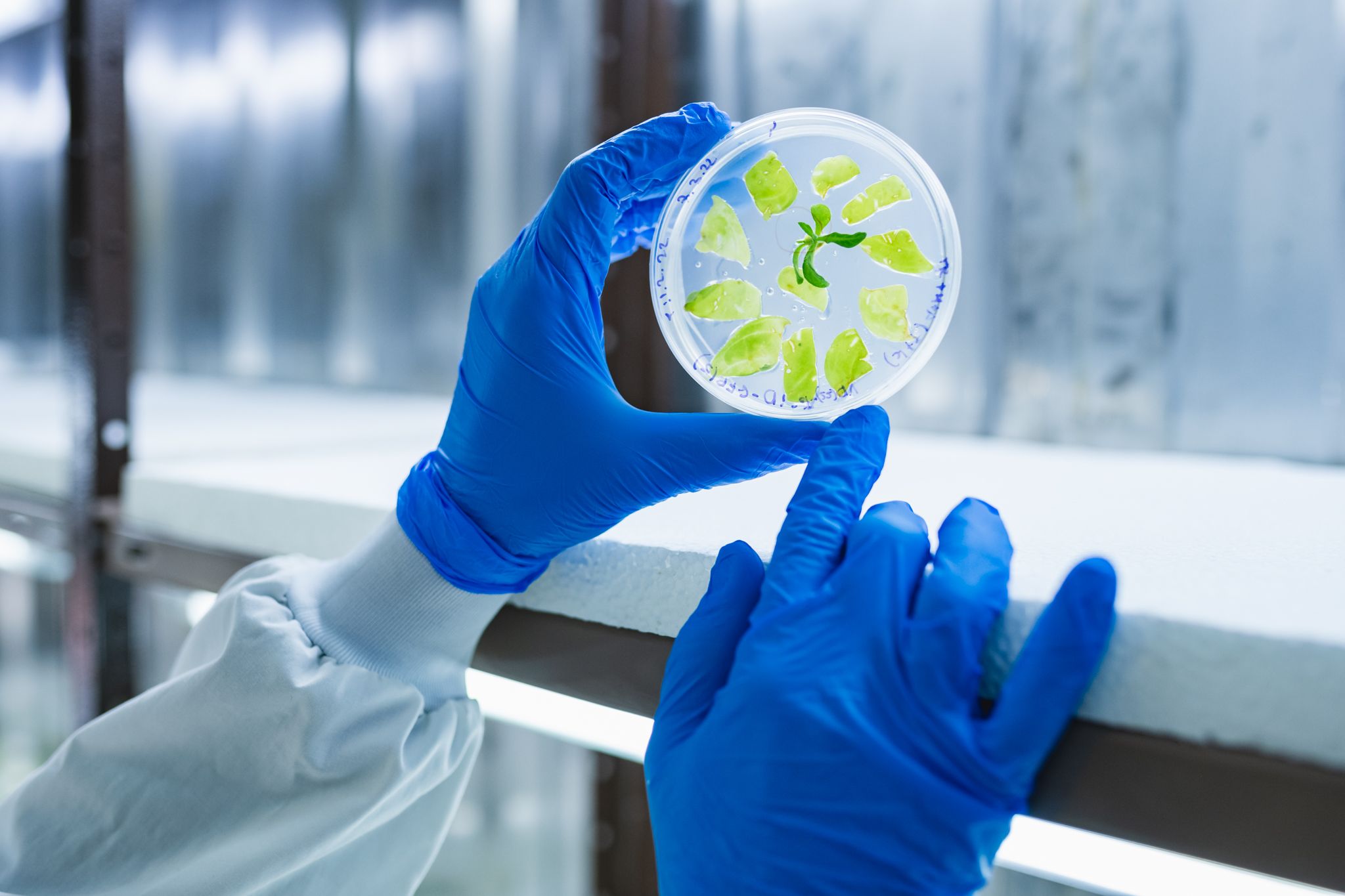
As well as drastically reducing costs, BioBetter also helps to substantially increase production scales while the growth factors themselves enable producers to form structured pieces of meat such as steak. “We have already produced four active growth factors and are now in collaboration with cultivated meat companies, media producers, and other cell ag developers,” Yarden notes. “Our main goals for the next 12 months are to establish a food production facility capable of producing 100kg of tobacco leaves per day, achieve self-affirmed GRAS status for two or three of the growth factors that we produce, and start getting the products into the hands of cultivated meat companies.”
The road ahead will not all be plain sailing, however. The transition from pilot to industrial scale in a manner that is both efficient and consistent is one of the big challenges for Yarden and her colleagues to tackle, although it’s one they are relishing. “Following significant progress made in meeting internal objectives and in addressing regulatory issues, our focus is now on scaling up rapidly to enable the cultivated meat sector to grow and thrive,” she says. “Scaling up efficiently and sustainably will be critical for the long-term success of the company.” Can BioBetter achieve those ambitions? “We are committed,” Yarden asserts, “and we’re exploring various approaches and strategies to achieve our goals.”
The alternative proteins sector is awash with the talent and expertise to – given time – overcome any technological obstacles, and the BioBetter team is evidence of this. Yarden, though, believes industry-wide progression could be accelerated with a bit of a helping hand from the powers that be. “Governments can provide crucial funding and resources for the R&D stages, as well as regulatory support for the approval and commercialization of alternative protein products (fast tracks),” Yarden feels. Additionally, she notes, support from government bodies would help increase consumer awareness and acceptance of these products, as well as provide incentives for food companies to invest in alternative protein options.
Currently, it is important to maintain realistic valuations and investor expectations to ensure the long-term sustainability of the sector
This would have been welcomed in the past 12 months, especially – a year that has been mired by negative press, some company closures, and lower investment activity. Yarden believes the latter, in particular, is partly due to the high valuations of some companies before the economic downfall, which she says were simply unsustainable. “While the food-tech sector was hurt, it was not as severely impacted as other sectors,” she concedes. “Currently, it is important to maintain realistic valuations and investor expectations to ensure the long-term sustainability of the sector. What has been disappointing for me is the realization that the focus is often solely on financial gain, whereas the importance of alternative proteins for the survival of our planet used to be the main concern.”
However, despite the tumultuous past year, Yarden still sees many reasons are to be optimistic. “The alternative proteins sector plays a critical role in addressing the environmental and health concerns associated with traditional animal agriculture,” she says. “As more people become aware of the benefits of alternative proteins, the demand for new and exciting options will continue to grow. Furthermore, the positive energy and enthusiasm surrounding this sector are still very much alive, and I am confident that it will continue to thrive in the years to come.”
We want to highlight the potential of molecular farming to become a steppingstone for cultivated meat production, and in the future even replace fermentation in the production of alternative proteins
The organizers of The Future of Protein Production LIVE! are hoping this energy will transcend at the in-person event at RAI Amsterdam, at which Yarden will be highlighting the importance of the “pick and shovel” technologies – critical she feels to improving the cost effectiveness of production and ‘de-bottlenecking’ in precision fermentation and cell-culture sectors. This will subsequently help companies advance toward commercialization by improving efficiency and yield. Examples, she cites, include novel bioreactor designs, innovative media formulations, process automation, and – as far as BioBetter is concerned – continuing to develop new technologies to produce cost-effective growth factors on a large scale. “We want to highlight the potential of molecular farming to become a steppingstone for cultivated meat production, and in the future even replace fermentation in the production of alternative proteins.”
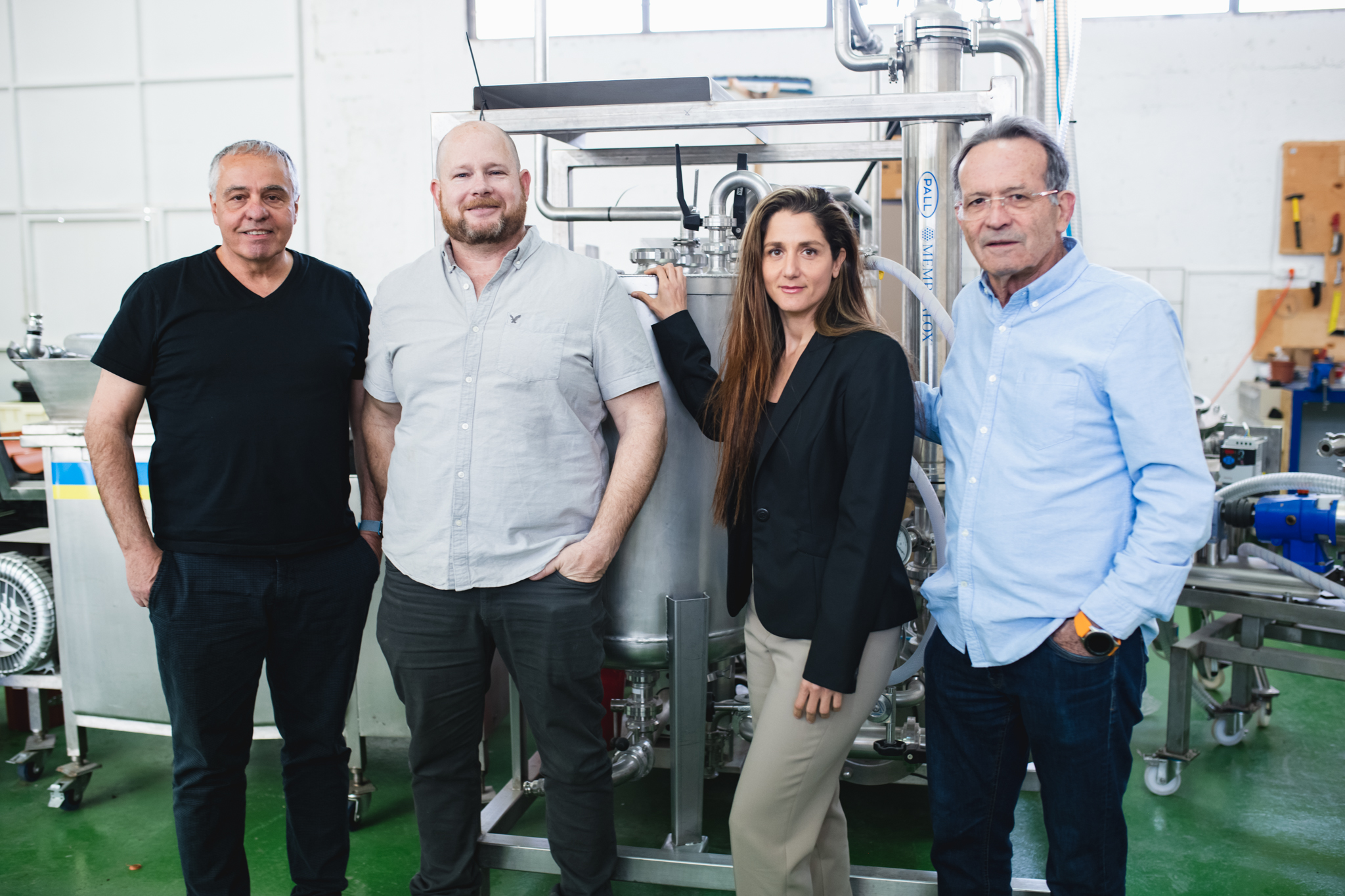
Yarden is certainly a glass-half-full type of person when it comes to the future. “The alternative protein industry is still in its very early stages, and currently represents only a small fraction of total protein sales,” she notes. “But the momentum towards plant-based and cultivated meat options is rapidly gaining steam, and I anticipate significant growth in the sector by 2030. For me, the regulatory approvals of UPSIDE Meat and GOOD Meat by the FDA have been truly significant breakthroughs. The fact the FDA had ‘No Questions’ about their GRAS submissions reduces one major hurdle for the industry – the regulatory risk – and signals that the US regulatory environment is supportive of cultivated meat. This is a positive step towards making cultivated meat a mainstream and accessible option for consumers.”
We may soon see 3D printers that can print customized burgers according to individual preferences. While this technology is still in its infancy, it has the potential to revolutionize the food industry in the coming years
As far as plant-based products go, Yarden believes tomorrow’s ‘Beyonds’ and ‘Impossibles’ will come to market with products featuring even better taste and texture. “Another trend that is likely to emerge is more traditional meat-based fast-food chains, such as Burger King, offering a wider range of plant-based options,” she predicts. “We have already seen some chains make moves in this direction, and I believe this will only continue as consumers become more conscious about their health and the environmental impact of meat. Furthermore, with advancements in technology, we may soon see 3D printers that can print customized burgers according to individual preferences. While this technology is still in its infancy, it has the potential to revolutionize the food industry in the coming years.”
Yarden is convinced that BioBetter will be a key part of that future food ecosystem. “I am proud of our company for being able to position itself as a key player in the food-tech sector within just two years,” she says of her achievements. “Once we achieve our goal of producing growth factors at a cost of US$1 per gram – which we are actively working toward – I will be extremely happy to be remembered as part of the solution that enabled this important Cell-Ag industry to become commercially viable.”
• Dr Dana Yarden is one of more than 65 speakers appearing at The Future of Protein Production LIVE!, taking place at RAI Amsterdam on 11/12 October. Click here to secure your delegate's pass and join more than 400 senior-level industry professionals to hear a fantastic agenda featuring 30 standalone presentations, take part in six engaging panel discussions, watch an exciting Startup Pitch Symposium and network with +30 exhibiting companies and other attendees
If you have any questions or would like to get in touch with us, please email info@futureofproteinproduction.com