
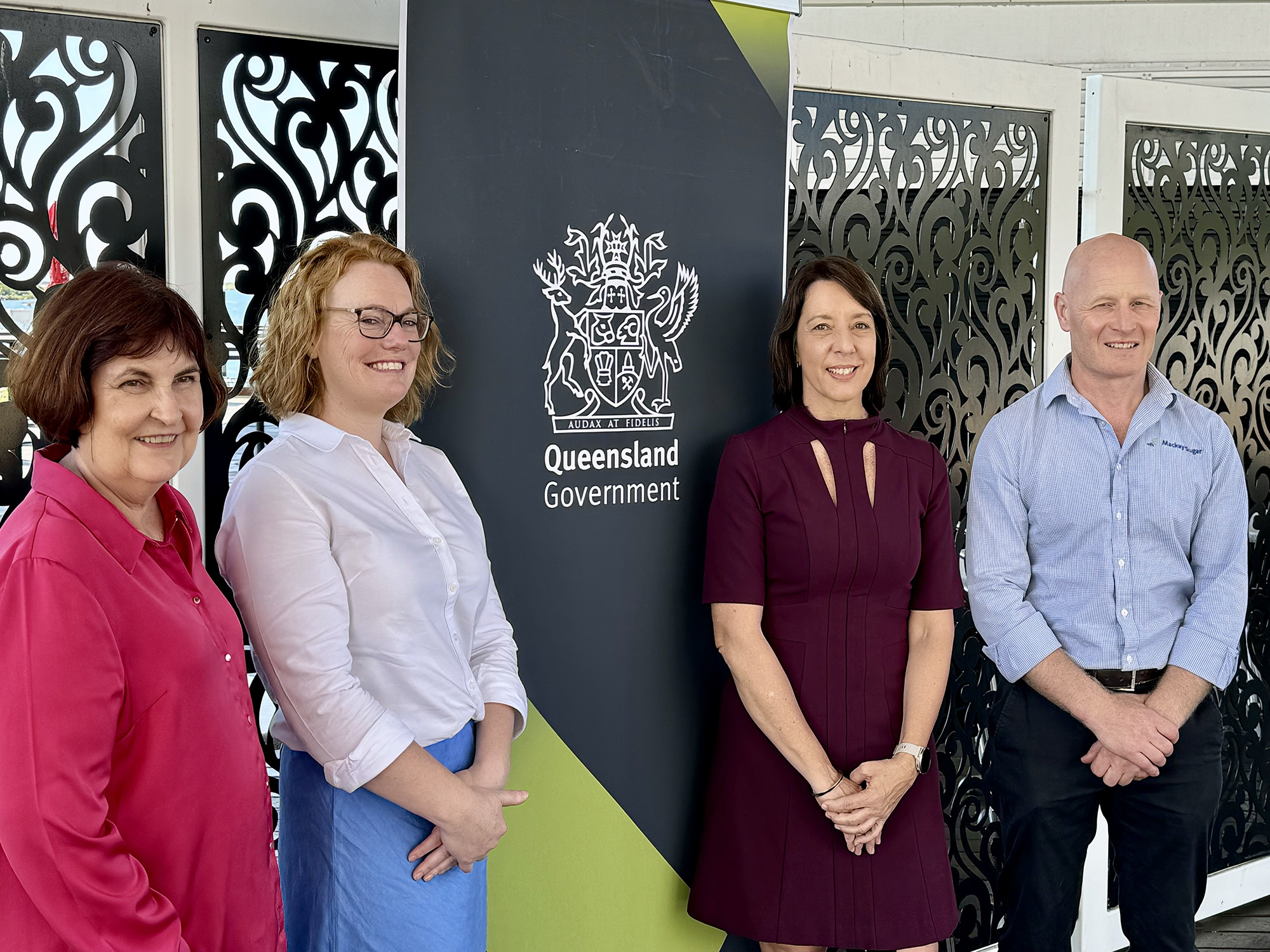
Cauldron moves forward with precision fermentation facility backed by Queensland government
Australia’s Cauldron, a biomanufacturer focused on scaling precision fermentation, has secured support from the Queensland Government to develop a new facility in Mackay. This plant will be the first of its kind in the Asia-Pacific region, designed to produce bioproducts on an industrial scale. With the Queensland Government’s backing, Cauldron aims to contribute to national resilience by improving biomanufacturing processes and addressing the increasing global demand for more sustainable production methods.
At the heart of Cauldron’s operations is its hyper-fermentation technology, which allows for cost reductions while maintaining productivity. Michele Stansfield, Co-founder and CEO of Cauldron, explained that this technology is the result of decades of research and development. “Our proprietary hyper-fermentation technology drives significant gains in productivity, generating more volume at less cost, using a more efficient bioprocess. These productivity gains unlock the volumes and cost of goods needed for bioproducts to achieve commercial traction in mainstream applications.”
By focusing on improving efficiency through a continuous process, Cauldron’s technology makes precision fermentation more accessible and economically feasible across a range of sectors, including food, nutrition, chemicals, and biofuels. “This technology is not just an improvement over existing processes; it represents a fundamental shift in how biomanufacturing can be applied across industries.”
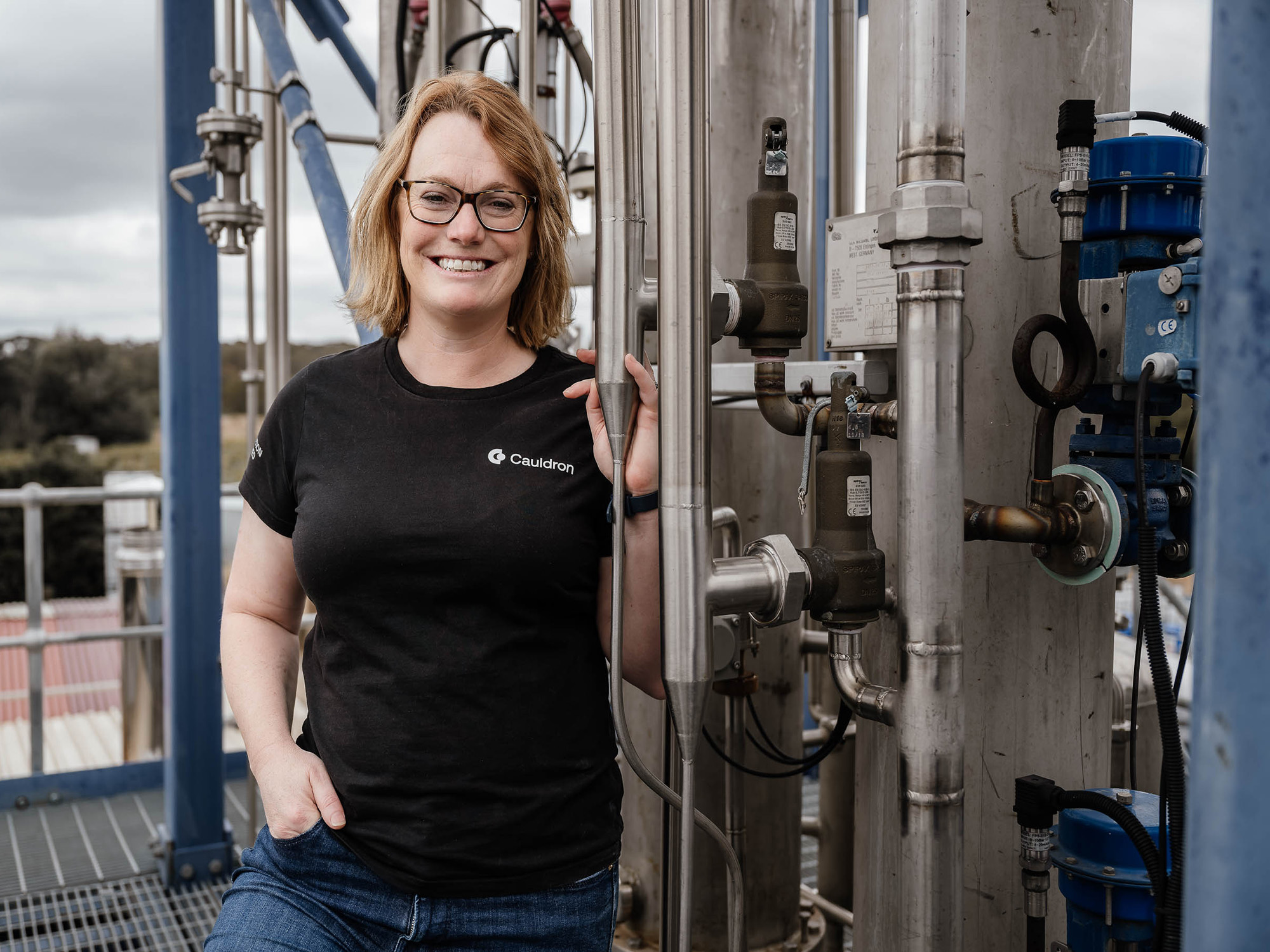
The Mackay Bio-fab is set to produce more than 1,000 tons of bioproducts annually, a significant increase from the company’s current 25,000-liter demonstration facility in New South Wales. Although Stansfield acknowledges that the transition from demo to full-scale production requires careful planning, Cauldron is well-prepared. “Our team has +10 years’ experience in the scaleup and commercialization of hyper-fermentation at our demo facility,” she said. “We’re confident that this robust foundation of operational excellence prepares us to scale to industrial production.”
In addition, Cauldron has assembled an experienced leadership team to support this scaleup. “We’ve brought on an experienced leadership team, including Chief Technology Officer David Weiner and Head of Operations Saurabh Das, who respectively bring deep expertise in scaling novel technology and in the design, build, and operations of industrial facilities.”
Increasing resource efficiency is essential for lowering production costs and reducing environmental impact. In sectors where sustainability is becoming increasingly important, these gains can make a big difference. According to Stansfield, “Cauldron’s proprietary hyper-fermentation technology scales up any precision-fermented prototype to commercial quantities more efficiently and at a significantly lower cost than traditional production methods.”
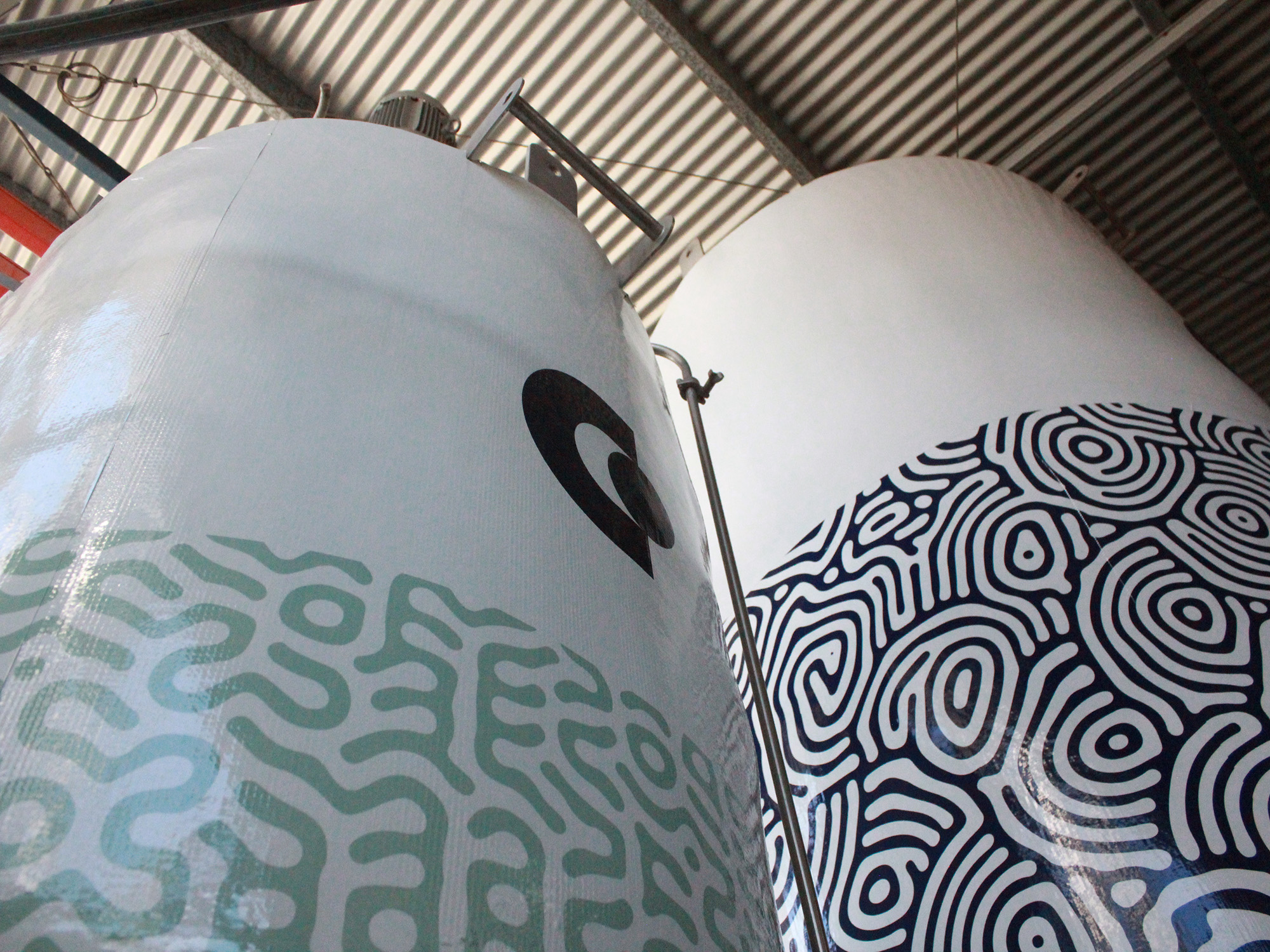
The process optimizes conditions for microorganisms to produce molecules, helping make bioproducts commercially viable. “This technology drives down cost of goods to achieve price parity with conventional products, making bioproducts commercially viable in a range of sectors,” Stansfield said.
Beyond cost efficiency, Cauldron’s hyper-fermentation also contributes to more sustainable production practices. “The process creates optimal conditions for microorganisms to produce new proteins, fats, and fuels, which makes bioproducts not only cost-effective but also resource-efficient.”
The Mackay Bio-fab is positioned to supply a broad range of industries, from food and nutrition to personal care and biofuels. Although this diversity offers opportunities for growth, it also requires careful adaptation of precision fermentation to meet the specific needs of different sectors. Stansfield pointed out that Cauldron’s platform is designed to handle multiple applications by focusing on secreted products from yeast, particularly using the microorganism Pichia pastoris. “For precision fermentation products across industries, our platform is compatible for secreted products from yeast, regardless of end-market applications.”
One of the advantages of Cauldron’s platform is that the bioprocesses can be adapted for different products with minimal changes. “For fuel and protein production from yeast, the biomass creation process is similar. In particular, the media remains the same at the microorganism level from one customer to another using the same Cauldron ACE model.”
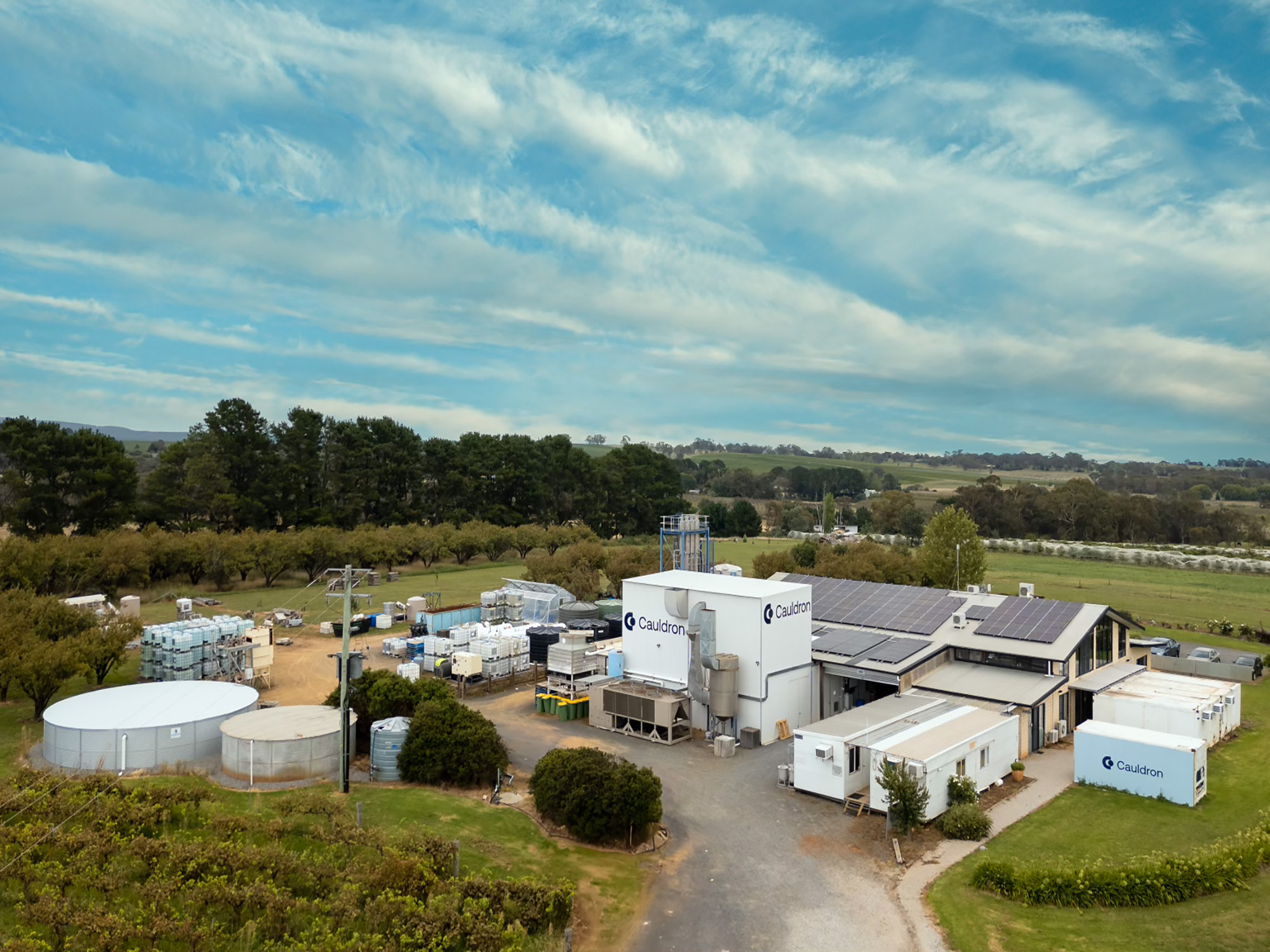
Cauldron’s demo facility in New South Wales plays a crucial role in ensuring consistency across sectors by allowing customers to validate the technology and optimize their processes before scaling up to full production. “It allows us to onboard customers to the hyper-fermentation platform, validate the benefits of the technology, and optimize the process for their strain at 10,000 liters before we scale up to industrial production at our Bio-fab,” Stansfield added. This approach minimizes risks associated with scaling and helps ensure that the final product meets the necessary quality and performance standards.
One of the most pressing global challenges today is ensuring food security in the face of a growing population and increasingly strained natural resources. Biomanufacturing, particularly through precision fermentation, offers a way to produce more protein and other essential nutrients sustainably. “By 2050, it’s estimated there will be an extra two billion people on the planet to feed. Coupled with changing tastes and dietary preferences, there is a growing demand around the world for more protein that is produced more sustainably,” Stansfield explained.
Cauldron’s technology not only addresses the need for more efficient food production but also strengthens the resilience of the food supply chain. By producing essential bioproducts locally and reducing reliance on traditional agricultural methods, biomanufacturing helps mitigate risks associated with climate change, crop diseases, and supply chain disruptions. “Precision fermentation diversifies the food supply chain, making Australia more food secure and resilient in the face of shocks whether from climate or geopolitical tensions,” said Stansfield.
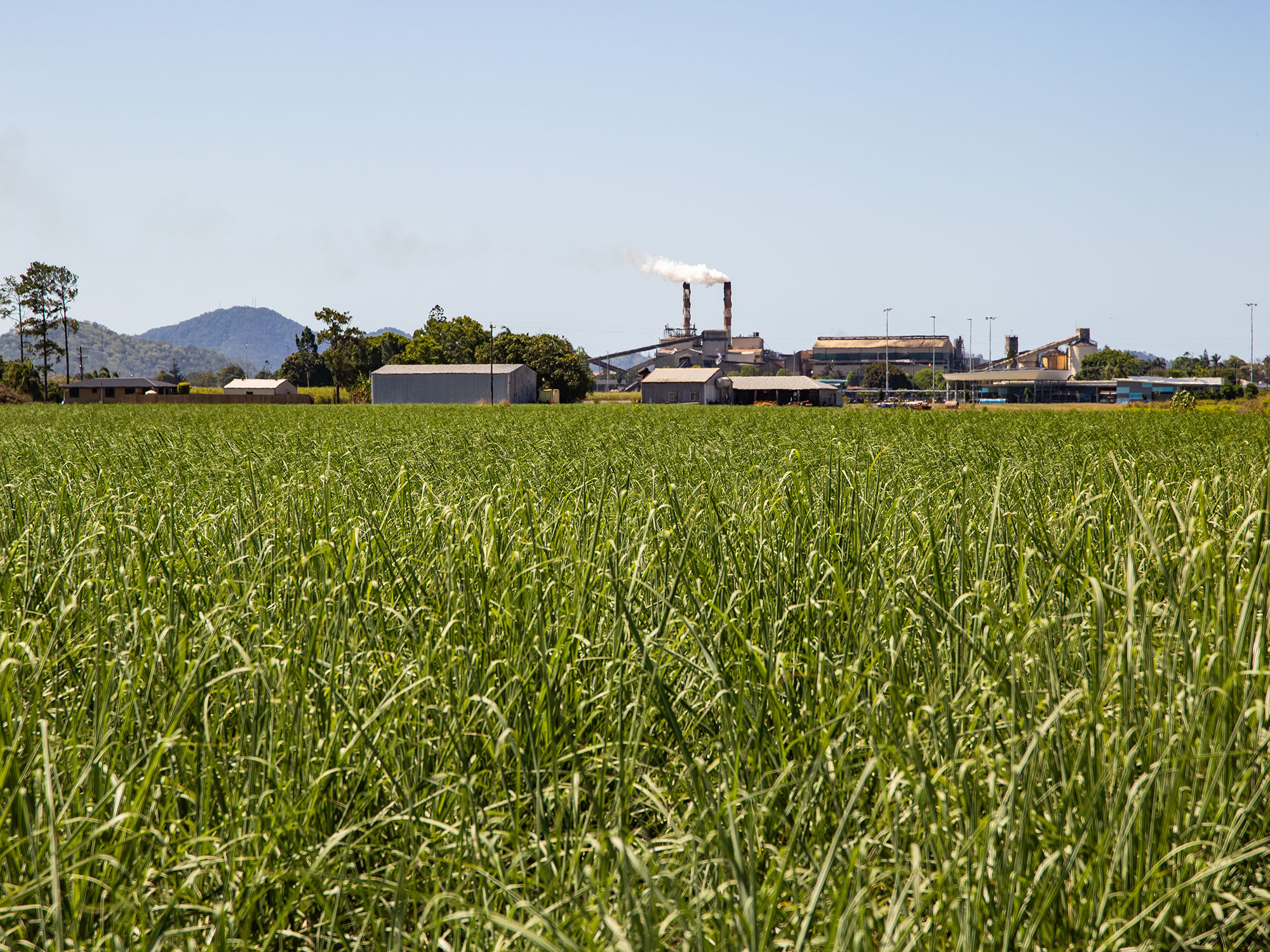
Although the Mackay Bio-fab represents Cauldron’s first large-scale facility, the company has ambitions to expand beyond Australia and develop a global network of biomanufacturing plants. As Stansfield noted, the demand for sustainable bioproducts is not confined to Australia, and the company sees potential for its technology in many regions around the world. However, expanding internationally requires careful consideration of regional bioeconomy needs and regulatory frameworks. “In engaging with different governments, we see consistent drivers for interest in biomanufacturing in terms of diversifying regional economies, creating high-demand, high-value products, and supporting new job creation.”
Each facility will be designed to adapt to local conditions, but the underlying principles of efficiency, sustainability, and scalability will remain central to Cauldron’s operations. Stansfield hopes that more countries will develop supportive regulatory frameworks to encourage the growth of biomanufacturing, much like Australia has done.
Cauldron’s hyper-fermentation process also contributes to decarbonization efforts in industries like food production. The platform’s resource-efficient processes reduce the overall carbon footprint by using less electricity, water, and land compared to traditional methods. “Techno-economic modeling shows that hyper-fermentation uses less electricity, water, and land compared to conventional fermentation methods,” Stansfield explained.
As more companies look for ways to reduce their environmental impact, Cauldron’s technology can play a role in making industrial production more sustainable. By enabling the large-scale production of bioproducts, the company is positioned to help industries transition to more climate-resilient models. “We see our role in the industry as an enabling technology platform that unlocks the scale up and commercialization of mainstream bio-products to reshape key sectors for a climate-resilient future.”
With the Queensland Government’s support, Cauldron is moving forward with the development of the Mackay Bio-fab. This facility marks a significant step in the company’s journey to scale precision fermentation, with the potential to play a key role in the global bioeconomy. As Cauldron expands its operations, it will continue to focus on efficiency, sustainability, and scalability, providing the infrastructure needed to meet the growing demand for sustainable bioproducts.
(Main picture shows from left to right, Julieanne Gilbert, Member for Mackay and Assistant Minister for State Development, Infrastructure, Industrial Relations and Racing, Michele Stansfield, Co-founder & CEO, Cauldron, Belinda Hassen, Candidate for Mackay, and Robin Stinson, Chief Financial Officer, Mackay Sugar, representing Australian Sugar Milling Council)
If you have any questions or would like to get in touch with us, please email info@futureofproteinproduction.com