
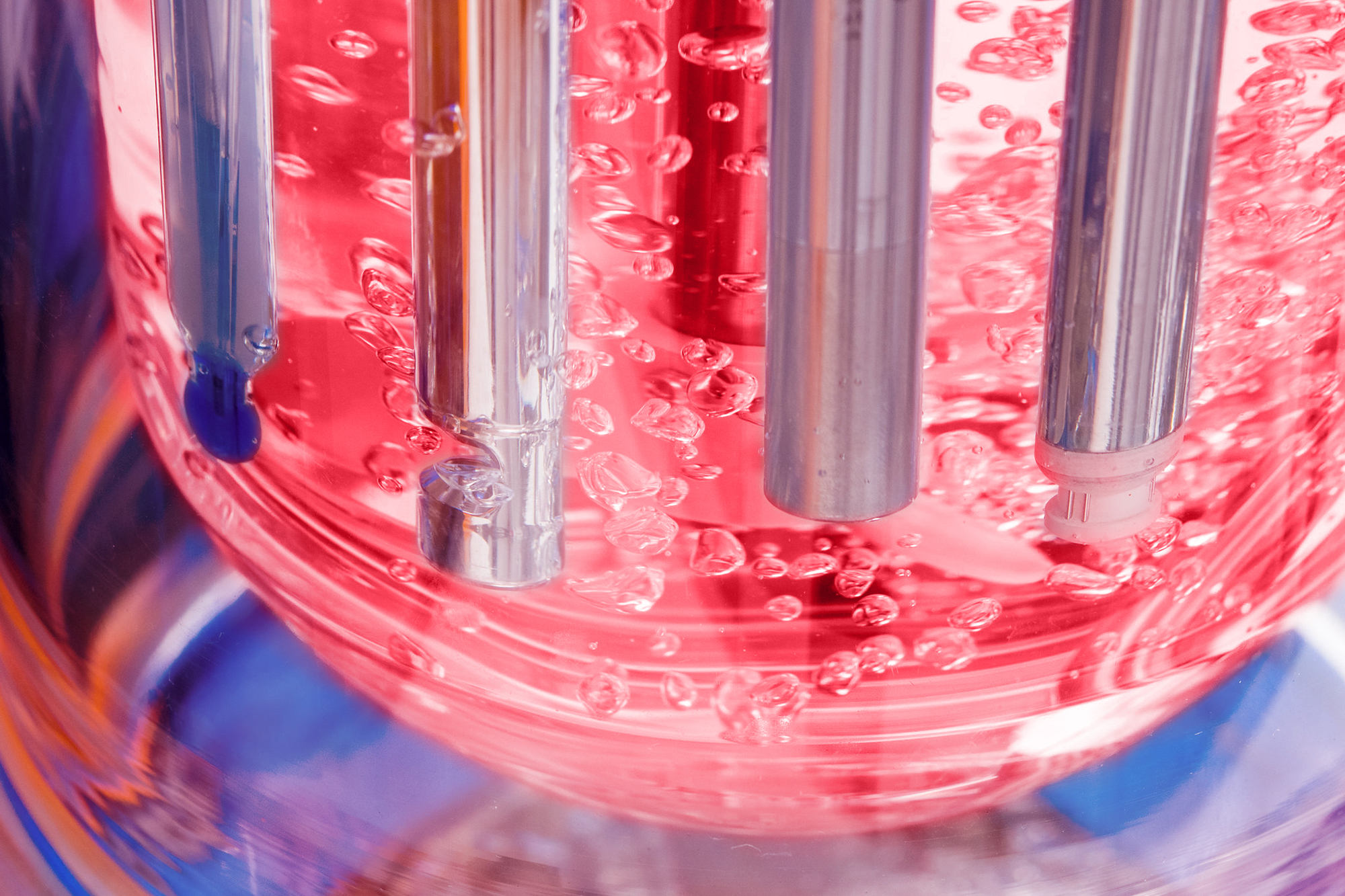
Measuring the future: the impact of Process Analytical Technology on cultivated meat
Jacob Crowe explains how – by utilizing Hamilton’s advanced sensor technologies – companies can optimize their media preparation process, ensuring consistent and efficient production of high-quality cultivated meat products
For cultivated meat to become a sustainable and ethical alternative, significant challenges need to be addressed. “Firstly, we must ensure that the cost of the production process is competitive, ideally at parity with traditional meat production,” begins Jacob Crowe, Applications & Tech Support Manager – Process Analytics at Hamilton Company. “Secondly, consistency in the quality of the product is paramount. Thirdly, customer acceptance is key; people need to recognize that cultivated meat is virtually indistinguishable from conventionally farmed meat.”
.png)
At Hamilton, the focus is largely on the cost aspect. “This entails aiding in the development of robust cell lines, reducing the consumption of media (one of the more expensive variables in the commercialization process), and assisting in the design of a production process that not only enables the growth of meat but does so at scale and with economic efficiency,” Crowe reveals.
“We must also consider the size factor. To make a meaningful impact compared to traditional meat, it might necessitate enormous facilities and potentially a substantial workforce unless we can devise an automated continuous processing strategy to limit footprint and manpower needs.”
Successful scale-up initially demands the development of optimized bioprocesses that exhibit robust and consistent performance, achieved through the effective implementation of good process control strategies. Process Analytical Technologies (PAT) present one control strategy based around critical parameters, with optimization of these parameters leading to a consistent process throughout the process development life-cycle.
Comprehensive solutions
Hamilton’s in-line sensors, including those for viable cell density, pH, dissolved oxygen, dissolved CO2, can play a pivotal role. “Firstly, our measurements have the potential to enhance environmental consistency, particularly in the upstream growth process,” Crowe says. “Secondly, we offer direct measurements of critical variables that impact cell growth, applicable to animal cell growth, bacterial fermentation, and more. Thirdly, our technology enables you to develop precise control mechanisms for these crucial parameters. Without it, decision-making would be limited to discrete choices or indirect inferences, relying on other, possibly less robust data outputs.”
Going into more detail about the parameters monitored by the sensors, Crowe breaks it down into three main areas: environmental parameters, nutrient monitoring, and cell measurement. “Key parameters like pH and oxygenation are critical for maintaining consistent environmental conditions,” he says. “These factors are crucial in aerobic processes, which are often the focus of cultivation. Aerobic environments are necessary for nearly all animal cell growth.”
Delving deeper into the importance of pH and DO control in bioprocessing, Crowe says pH is critical. Maintaining a precise pH range is essential for achieving consistent and reproducible results, while deviations from the optimal pH range can lead to altered metabolism, slower cell growth, and reduced productivity. “Over time,” he points out, “pH measurements can drift, which will impact the process’s stability and performance. It’s vital to monitor and mitigate pH drift to prevent detrimental effects on both metabolism and the overall process, especially in long-running processes.” DO control, meanwhile, is essential for providing the right amount of oxygen to support cell viability and growth in aerobic processes. “Although hitting a DO setpoint is important, the stability of that setpoint within a specific range, such as plus or minus 5% saturation, also plays a crucial role in process quality and consistency,” Crowe advises.
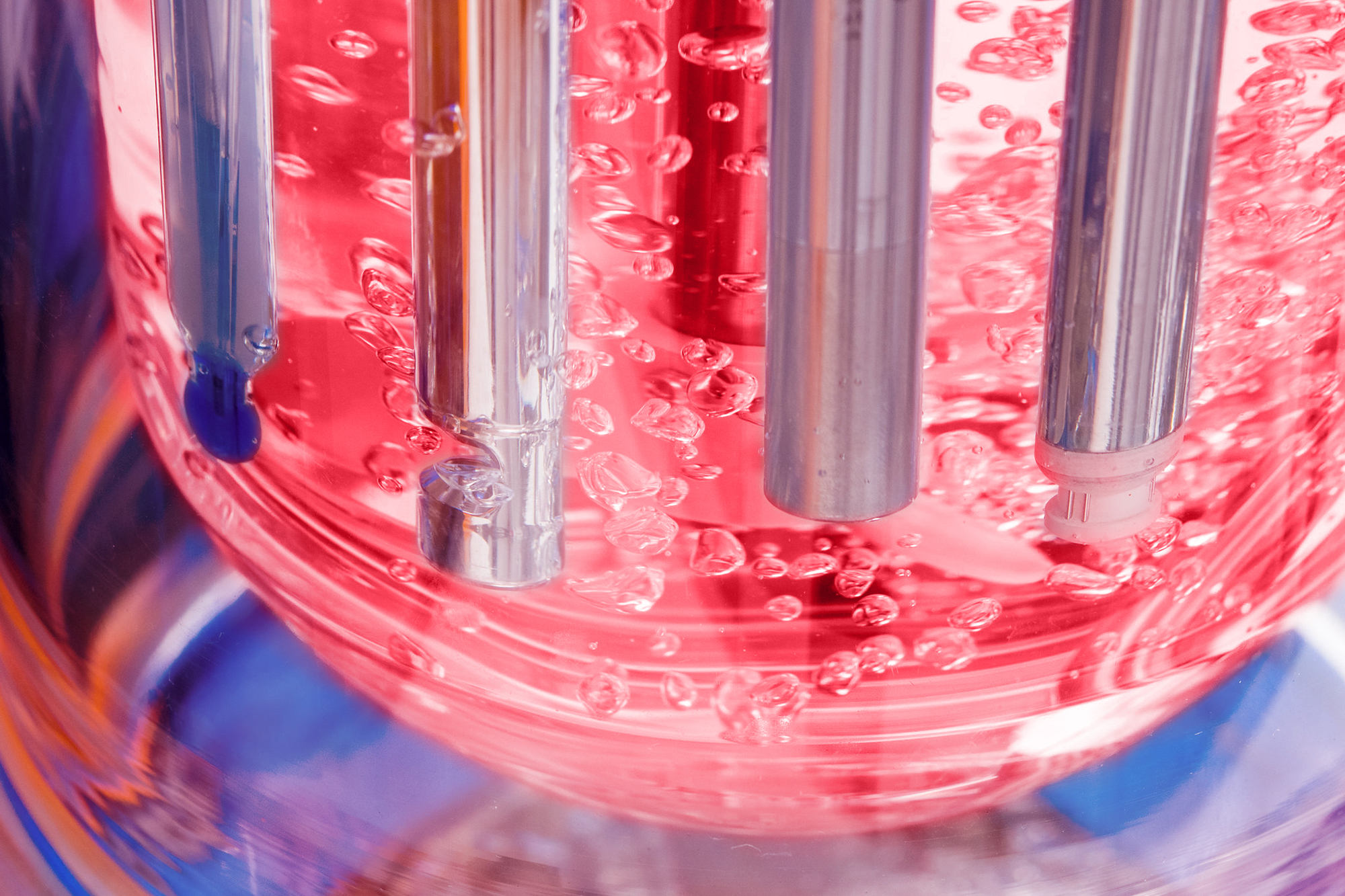
“The method used for DO control and measurement can impact the reproducibility and yield of a run. Noise or instability in the DO control can lead to variations in process outcomes, despite maintaining DO levels at a target setpoint.”
As far as nutrient control and feed strategies are concerned, Crowe says there are two routes: direct metabolite measurement and measurement of cell concentration, or overall biomass within the process. With the former, the approach involves directly measuring metabolites, typically through enzymatic assays or spectroscopy techniques. “Over time, you track how specific nutrients are depleted from the culture,” says Crowe. “Based on this data, you can design a targeted feed strategy to supplement the depleted nutrients. This method provides a cost-effective way to understand and replace essential nutrients, such as amino acids and growth factors. However, it may not be feasible to measure and supplement every nutrient individually due to practical limitations like the number of feed pumps and inlets.”
In relation to biomass measurement, you directly measure the growth of the cell population, most often using a metric for viable cell concentration (VCD). “By mapping out the metabolic requirements for primary cell growth or maintenance, you can estimate nutrient requirements for a viable cell concentration over a period of time,” Crowe explains. “Over a defined process duration, you measure cell growth and then either empirically calculate the nutrient requirements or use predefined models. This method is useful for large bolus feed additions, as seen in fed-batch strategies or in continuous media replacement strategies, such as perfusion control. It allows you to estimate and replace the nutrients consumed by the cells during the specified time frame.”
The ability to continuously monitor VCD in real-time is significant. In cultivated meat, precise and ongoing assessments of VCD are indispensable throughout the culture process, given that the cells themselves are the end product.
“The power of real-time data lies not only in continuously observing signals but also in the ability to control processes based on that data,” notes Crowe. “All our measurement solutions offer output signals that enable integrated control. For instance, consider a pH sensor; it’s seamlessly integrated into a continuous feedback control using base and acid feed controls, eliminating the need for discrete intervention and in so doing, reducing the human element of process inconsistency.”
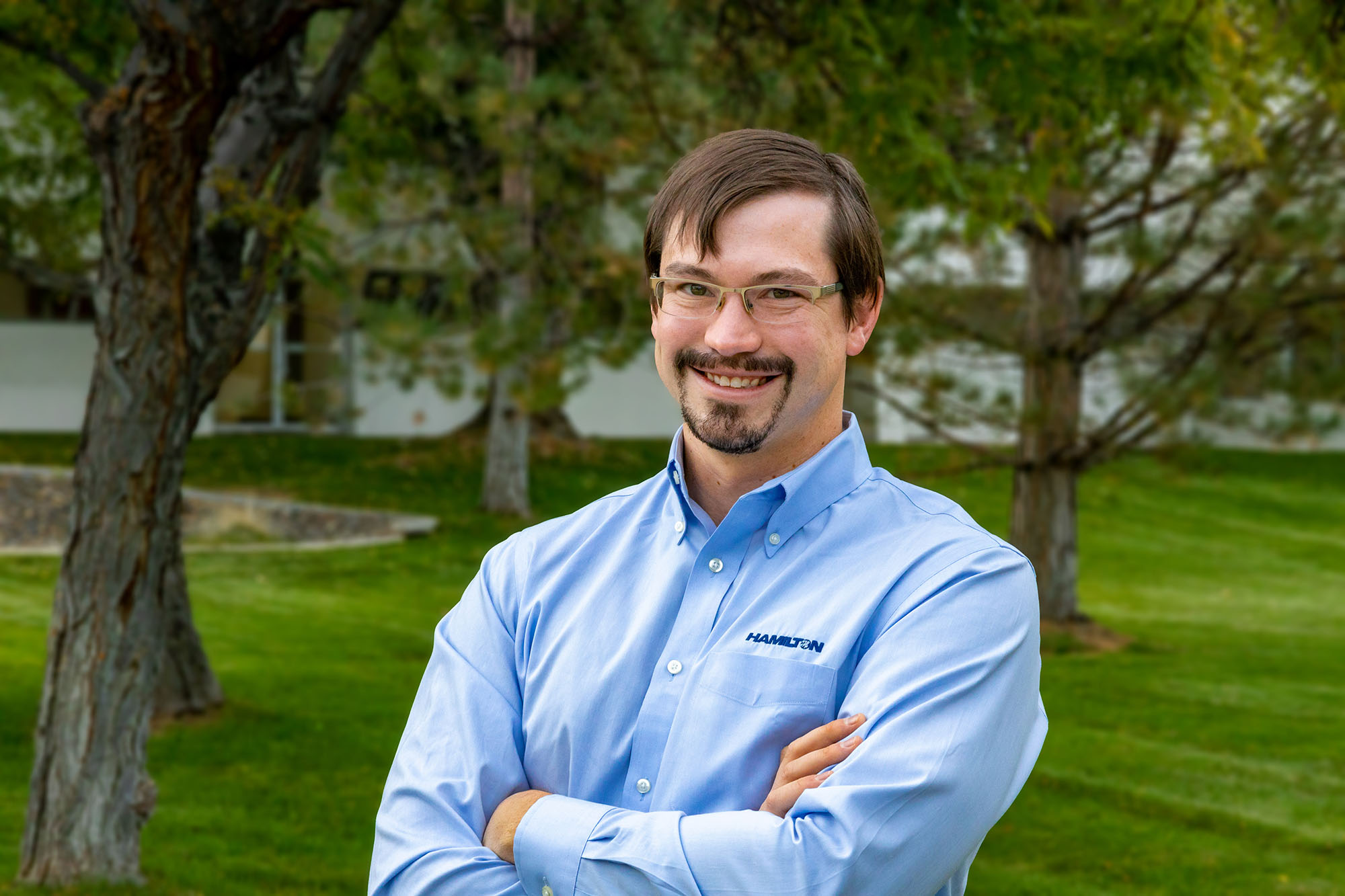
“As the cultivated meat industry matures and larger facilities emerge, automation becomes pivotal for economic feasibility
In the case of an in-line VCD measurement, Hamilton’s capacitance sensor directly measures viable cell concentration, offering a direct signal for controlling processes based on the amount of viable cells. “In the cultivated meat industry, there are two prevailing directions: large tanks or continuous processing,” Crowe says. “With continuous processing, having direct control over your product (the viable cells) becomes crucial. This measurement enables the development of control schemes such as cell bleed, or the removal of a certain cell volume from the bioreactor at any given time, allowing for ongoing operations instead of letting cells grow to full capacity before harvesting. This is almost a necessity for implementing such processing strategies.”
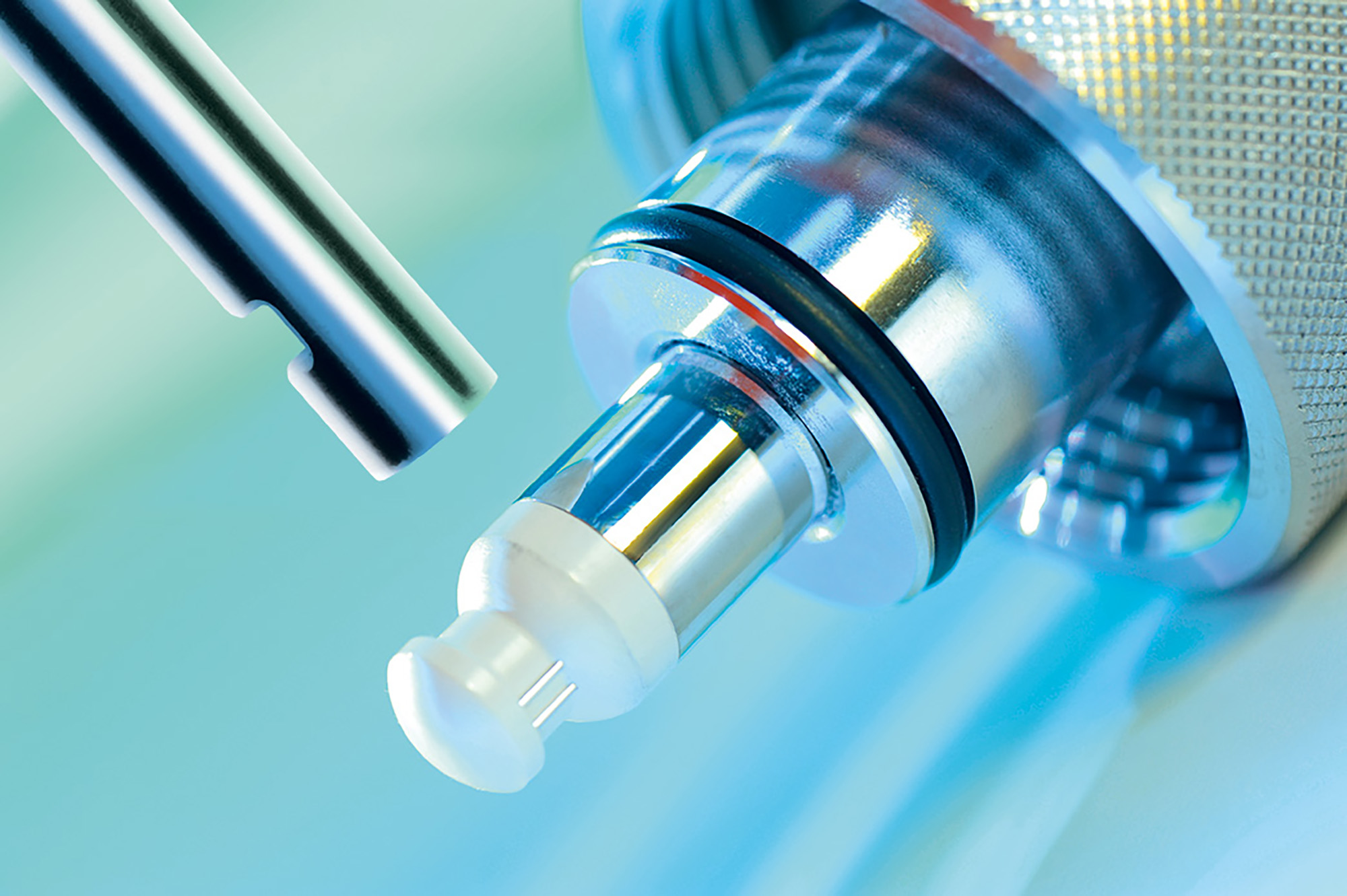
Contamination is also a vital but overlooked challenge. How can Hamilton’s technologies help here? “Ensuring a contamination-free environment is paramount, and in cases where contamination does occur, rapid detection is essential,” Crowe says.
With inline measurements and a well-defined batch profile, maintaining tight control over the process is vital. “Any deviation from the ideal batch conditions or the ‘golden batch’ profile can be quickly identified when contamination or anomalies arise. So, an inline control system is beneficial in detecting deviations faster than relying solely on discrete offline sampling.”
An absolute imperative
Ultimately, the implementation of process automation via PAT and in-line sensors is imperative for the prosperity of cultivated meat production, especially given the narrow profit margins typically associated with the food industry.
“When we consider the scale required to make a significant impact in the cultivated meat industry, it becomes evident that a substantial labor force will be necessary,” Crowe suggests. “However, this reliance on manual labor can drive up operating costs. Wherever possible, automating processes reduces these costs and minimizes potential sources of error.
“Using measurements to enable automated processes – such as feed transfers or cell bleeds – removes the human factor and its associated costs,” Crowe details. “As the industry matures and larger facilities emerge, automation becomes pivotal for economic feasibility and maintaining a consistent and reproducible product with minimal errors.”
Hamilton is already collaborating with a wide range of groups in the cultivated meat industry, from small-scale operations to those working on pilot-scale and developing commercial production plants.
“We are committed to providing support for any PAT needs that our customers, both existing and new, may have. We take pride in our strong support structure and our dedication to facilitating face-to-face interactions,” Crowe says proudly.
“In the bioprocess industry, we have maintained a high standard of service, and we intend to uphold that same level of service in the cultivated meat sector.”
For more information about Hamilton products, please click here
If you have any questions or would like to get in touch with us, please email info@futureofproteinproduction.com